
In modern industry, the choice of materials often determines the success or failure of the project. And today's protagonist-aluminum wrought iron capital series is such a silent support from the construction, machinery and manufacturing fields of important role. This series not only inherits the tenacity of traditional metal products, but also achieves a leap in performance through innovative technology.
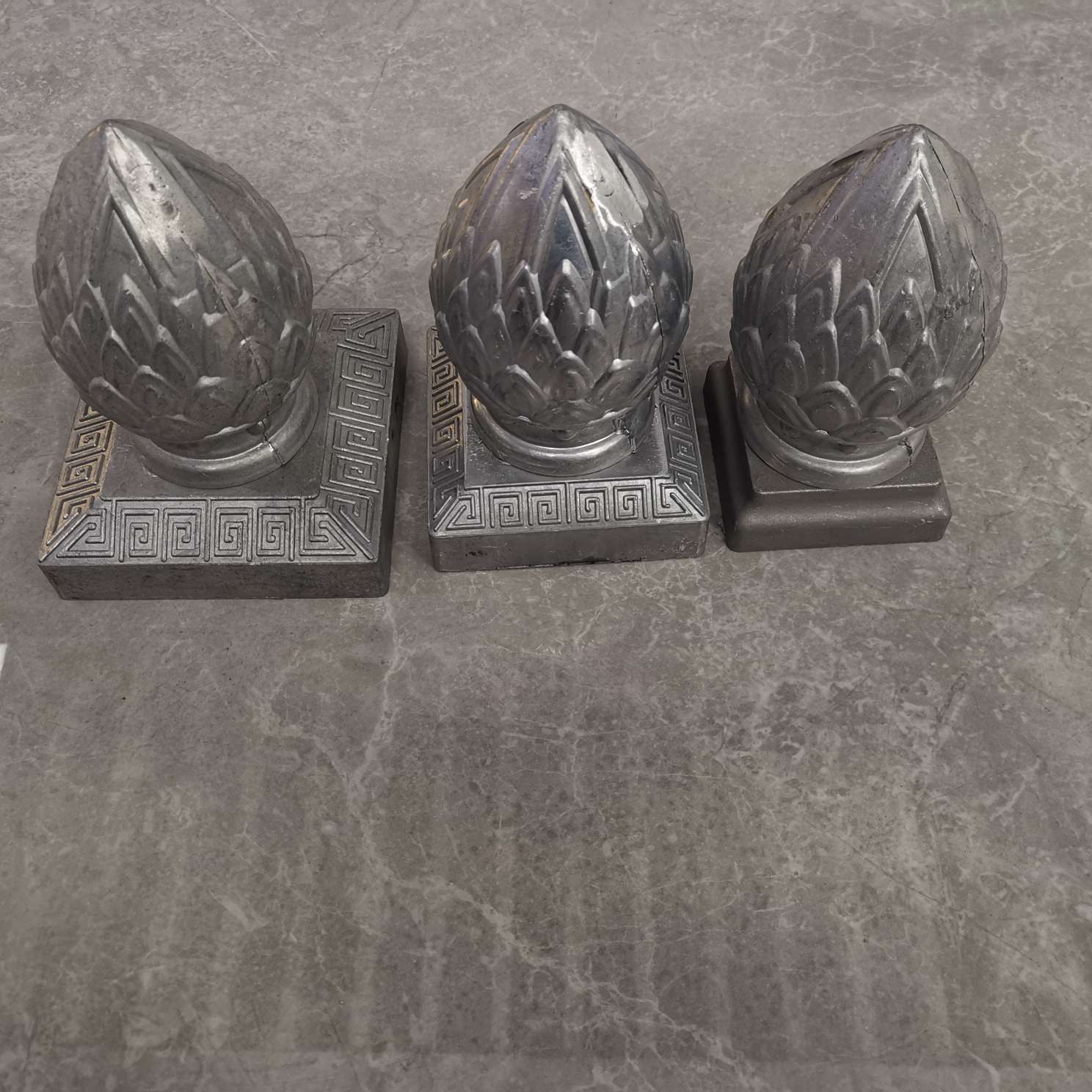
For application scenarios that require precise adaptation, the 80, 100 and 120 specifications undoubtedly provide great flexibility. Among them, the smaller size such as 80 is suitable for light equipment installation or precision parts connection; the standard model 100 is widely used in load-bearing structure reinforcement; as for the larger 120, because of its excellent carrying capacity to become the ideal choice for heavy machinery and equipment. Each has its own unique mission and plays an irreplaceable role in a particular environment.
So what makes these products so powerful? The answer lies in the fact that the underlying materials they use are inherently highly resistant to compression and ductility. Aluminum wrought iron combines the advantages of two elements, which can not only ensure sufficient hardness to meet the challenges of complex working conditions, but also maintain a certain degree of softness for processing and forming. This combination makes it stand out in the market.
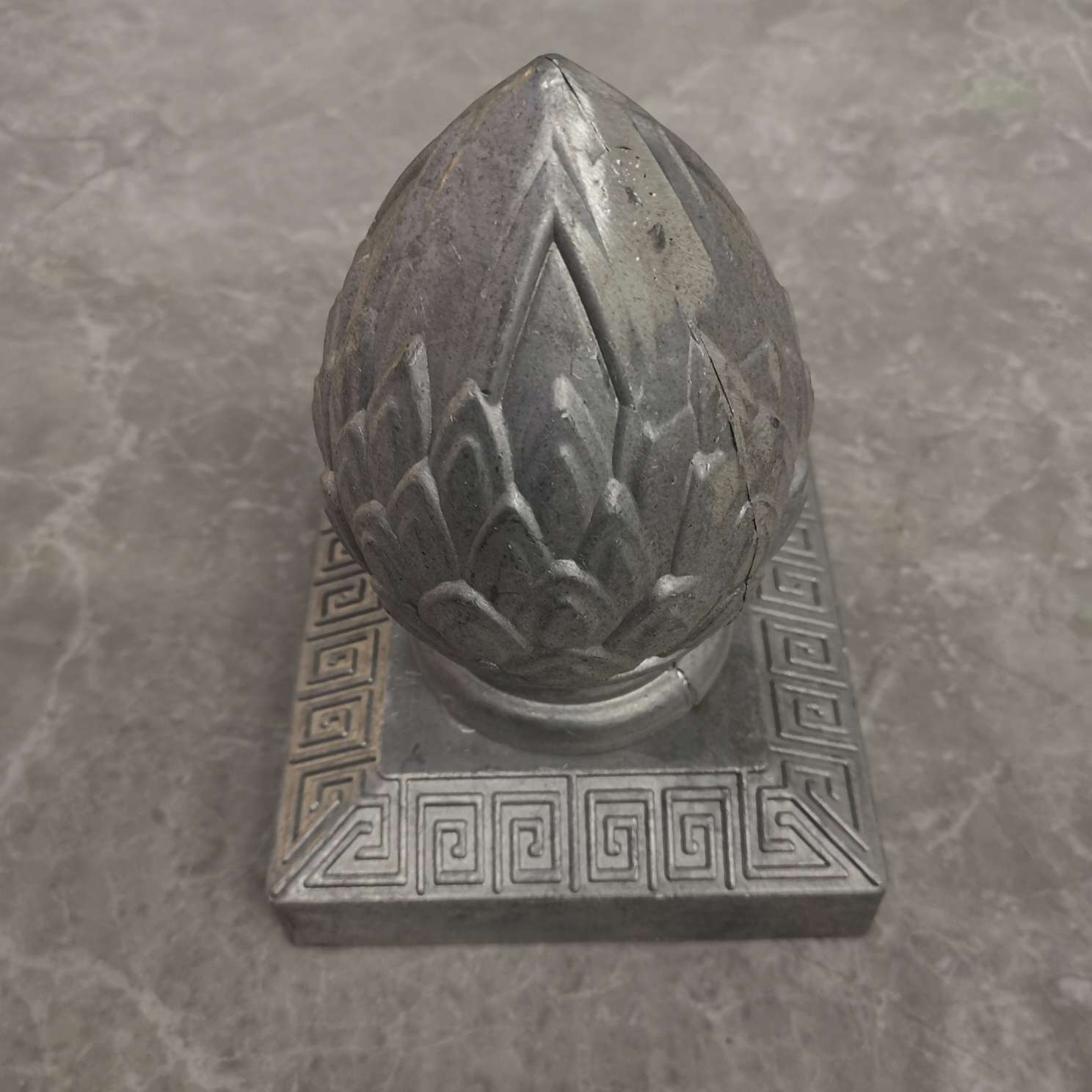
Of course, in addition to basic attributes, design considerations are also crucial. For example, the surface treatment process can significantly reduce the risk of corrosion and thus extend the service life; tolerance control accurate to the millimeter level ensures that each component can be seamlessly connected to other components to achieve a perfect match. All this is to give customers a more reliable and easy-to-use solution.
To better prove this point, please allow us to share a few examples from actual operations! A large-scale bridge construction project has selected our No. 120 aluminum forged iron column for key parts of the fixed work, the results show that the whole process is smooth and no abnormal situation has been reported. There are many similar positive feedback further confirmed that the excellent performance of this series of products is indeed worthy of the name.
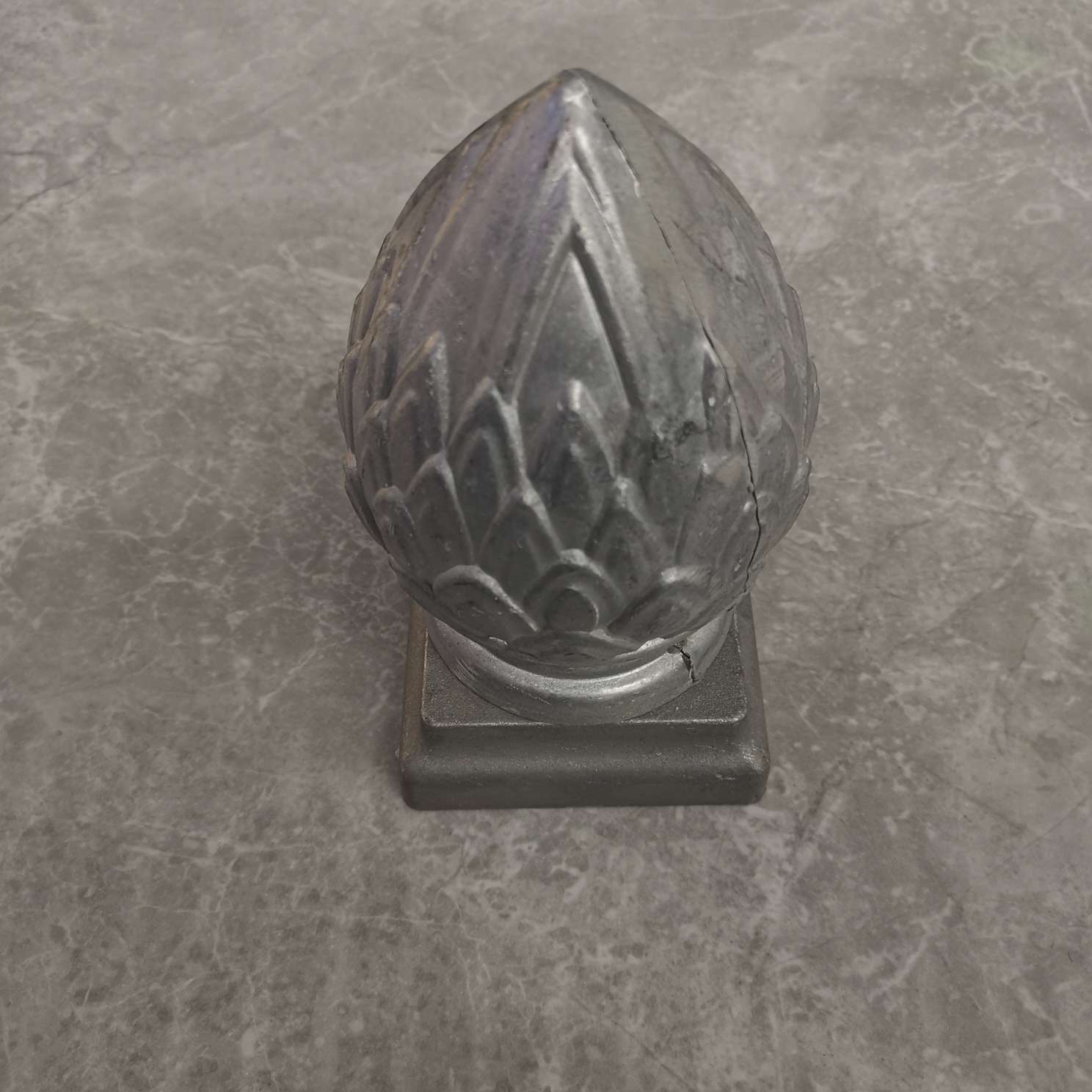
Although the product quality is excellent, reasonable maintenance is still essential. Regularly check whether the fasteners have signs of loosening and adjust the reset in time. It is a simple but effective way to apply protective coating to the exposed part to prevent the external environment from eroding. Following the above steps will greatly help you maximize your return on investment potential.
Looking to the future, with the continuous development and progress of science and technology, it is believed that the research around this kind of advanced composite materials will continue to deepen. Maybe one day we can see a new model that is stronger and more environmentally friendly than it is now, and start a new chapter! Let's look forward to this day as soon as possible.
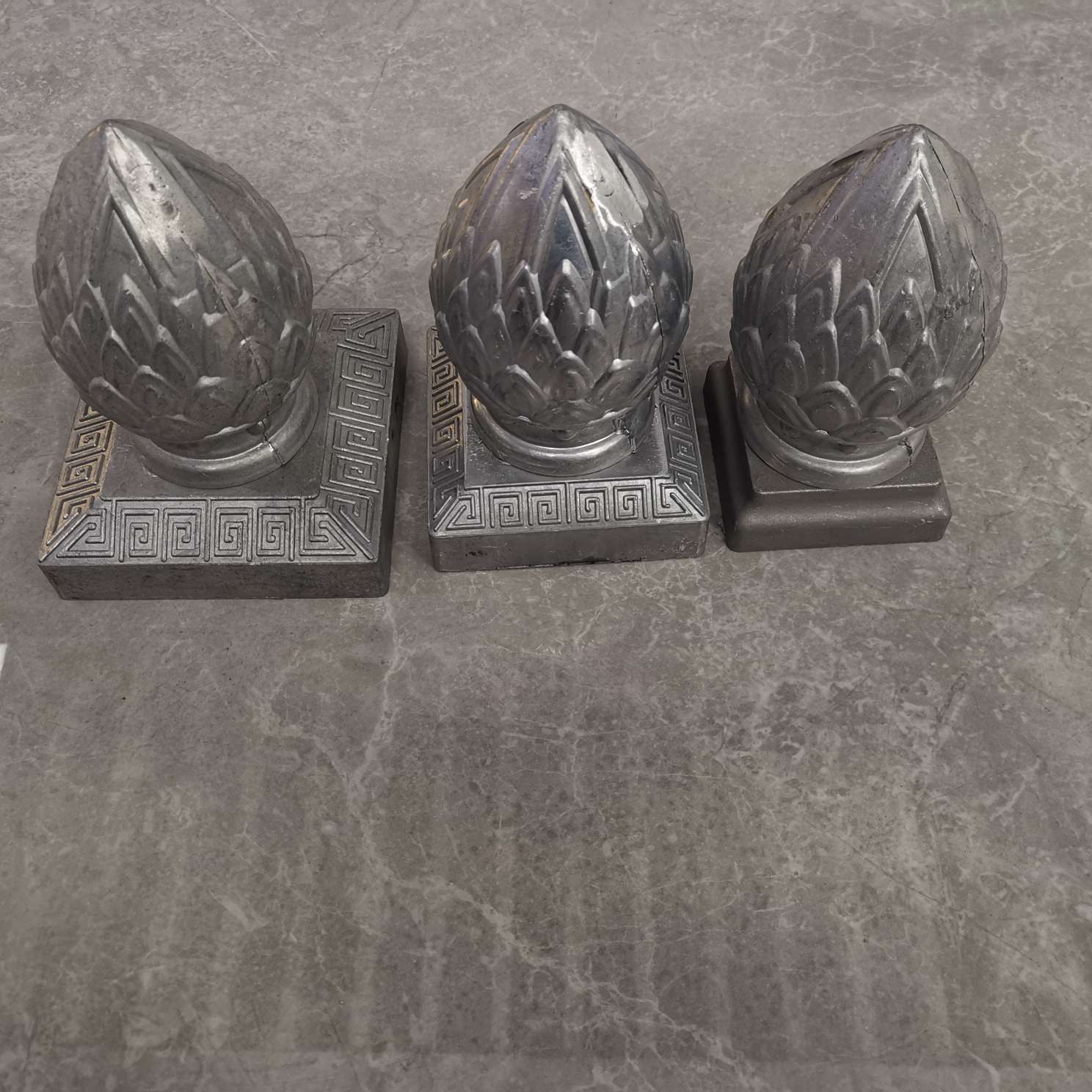